Epicor surveyed key stakeholders in the manufacturing sector about essential workers’ everyday experiences, pain points and expectations. Vibhu Kapoor, Regional Vice President – Middle East, Africa & India, Epicor, explains the five broad action points which companies could take, based on the findings from the survey.
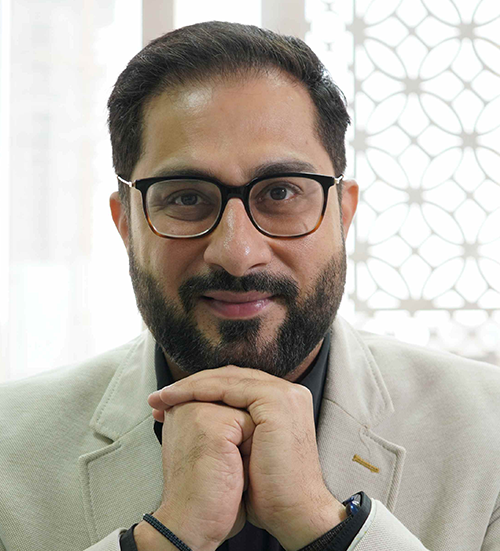
Amid regional initiatives such as the UAE’s Operation 300bn, manufacturing in the Middle East has been on an upward trajectory. This growth certainly owes much to the foresight of ambitious governments, but at its heart, it is driven by people. And not just boardroom strategists, but frontline workers.
In Epicor’s Voice of the Essential Worker: Manufacturing 2024, we surveyed key stakeholders in the manufacturing sector – engineers, machinists, welders and supply chain analysts making everything from food and furniture to apparel and electronics. We believe that to avoid the classic board/shop floor disconnect, you need to walk onto the floor and ask about essential workers’ everyday experiences, pain points and expectations. In doing so, we uncovered insight which can be applied to unlock the full potential of the manufacturing sector in the Middle East. Our findings, split here into five broad action points, should help the region’s industrial leaders to understand the source of morale and how to improve it.
Modernise
Just over a third (39%) described their company as ‘very modern’ and less than half (48%) said their company was adopting new technology. More than half (56%) said they would take a pay cut if it meant working in a more technology-driven environment. This reflects a reality shared by the Middle East – a workforce steeped in technology at home and at play and as they shop. They expect the same at work and are willing to look around for employers that will deliver.
In a region plagued by talent gaps, firms must act to provide stellar employee experiences. That is why, across the GCC, we see manufacturing companies moving to the cloud, which provides the security and agility to provide such experiences. Young workers respond positively to paperless factories where data reigns, tied together and intelligently managed by top-of-the-line ERP systems. Our respondents listed AI, robotics, augmented reality, big data and 3D printing as the top technologies adopted by their employers. ERP ties these capabilities together to give the factory floor workforce empowering insights that make them more productive.
Train
One heartening find in the study was that 70% said their employer was prioritising upskilling. Yet 43% were eyeing a job move this year and two-thirds (66%) said they would tolerate longer hours if it came with more upskilling. Again, we see this everywhere, including in this region. It is especially encouraging to see that young professionals want to learn so they can compete for new roles and build meaningful careers.
In manufacturing, no matter where you work, you grow alongside technology. Upskilling programmes must be business-driven. Train staff in new skills that will be applied to the adoption of a value-adding tool such as AI. The delivery plan should allow for both, on-the-job training and self-service online learning. And remember to measure the impact of upskilled workers and debrief them on their experiences as they apply their new skills, so you can make continual improvements to training.
Communicate
We found that failure to heed feedback was among the top five reasons for low morale in our cohort of respondents, who also judged poor communication to be the top attribute shared by subpar supervisors. Although cultural proclivities vary wildly between the surveyed region and the Middle East, everyone needs to be heard. In this region, we may need to come up with ways to encourage people to speak up in the first place. But feedback is how you discover what is right and what is wrong on the factory floor. Without it, you are blind.
So, head to the shop floor and ask for feedback. Assure the workforce that open doors are not merely for show. Establish a tradition of open dialogue at meetings and one-on-ones. Implement suggestion boxes. Cater to every personality type, from the shyest to the most outspoken. And once you receive feedback that is useful, act on it and share the results.
Accommodate
More than half of respondents (55%) said their morale was not high, citing a lack of raises and bonuses as top reasons. While it is not necessary to have every staff member come into work every day with a bounce in their step, morale must remain high on aggregate for a business to function well. Beyond monetary factors, perks can help, as can opportunities for professional development. But arguably the most significant non-monetary compensation for the modern worker is flexible working. This is more important to factory workers who see their back office colleagues working from home while the same is not available to floor personnel. Even the ability to choose a daily start and end time for a floor shift would be a boon.
Change
Most of our surveyed factory workers (55%) would take a pay cut to work at a more sustainable factory, while only 45% say their organisation is being proactive in this regard. In the wake of COP28, more workers across the region are looking to their employers to lead and align with their nation’s sustainability goals. To attract and retain young talent, firms must reduce waste throughout the manufacturing process. Technology tools are on hand to help, by analysing data and using AI to suggest more efficient processes, greener materials and more efficient consumption of energy. Technology can audit entire supply chains to identify vendors who have the same sustainability priorities and those that may need to be replaced.
What next?
Once something is named as a trend, those that are not part of the trend are already on the cusp of being left behind. If a firm understands what its workforce is going through, it is in a position to act. But only if it chooses action can it reap the rewards of a driven workforce. That workforce wants a sustainable, more technology-driven factory and enough flexibility and compassion to feel valued and supported. It’s now the time for Middle East industrialists to usher in the future of manufacturing.